Content
Introduction
Metal furniture is popular because it is durable, modern, and versatile. It can be used in busy spaces like banquet halls, hotels, or conference rooms. Metal furniture must not only be functional but also visually appealing and long-lasting. Making high-quality metal furniture involves many steps.
This article explains the manufacturing process of RON GROUP. It covers key steps from material selection to final coating and curing. It shows how metal furniture is made with care and precision.
Material Selection
The choice of material is important for how the metal furniture works. It also affects how long it lasts. Below are some common metals used for furniture and their key features:
Aluminum
-
Lightweight and corrosion-resistant
-
Ideal for outdoor furniture due to weather resistance
-
Available in multiple alloy grades, offering versatility
Stainless Steel
-
Durable, corrosion-resistant, and easy to clean
-
Suitable for kitchen or hospital furniture
-
Good weldability, making it easier to work with for complex designs
Wrought Iron
-
Heavy and durable but prone to rust without proper surface treatments
-
Used for decorative, antique, or outdoor furniture
-
Requires protective coatings to prevent corrosion
Brass
-
Anti-microbial and corrosion-resistant, with a distinctive appearance
-
Often used for decorative furniture and fittings
-
Adds an antique, luxurious touch to the final product
Shaping
The way metal components are shaped affects production cost, precision, and structural properties. Here are five popular metal forming processes:
Roll Forming
-
Process: Flat sheets are gradually bent into shape using a series of rollers.
-
Best For: Simple, symmetrical tubular components with consistent cross-sections.
-
Advantages: High efficiency and low cost for large-scale production.
Tube Stamping
-
Process: Sheet metal blanks go through several stages of stamping. This forms them into tubular or asymmetrical shapes.
-
Best For: Intricate shapes that require precise customization.
-
Advantages: Can handle complex designs and reduce production time.
Hydroforming
-
Process: A tube is placed in a mold and filled with pressurized fluid to shape it from within.
-
Best For: Complex, asymmetrical tubular shapes (e.g., automotive components).
-
Advantages: Allows for highly detailed shapes but is slower than other methods.
Casting
-
Process: Molten metal is poured into a mold and allowed to cool.
-
Best For: Unique, solid shapes or pieces with intricate detailing.
-
Advantages: Excellent for small batches but costly and time-consuming.
Machining
-
Process: Cutting, drilling, or milling metal into specific shapes using computer-aided tools.
-
Best For: Components with tight tolerances and precise dimensions.
-
Advantages: High precision but less suitable for mass production of complex shapes.
Preparing and Cutting
The first step in making metal banquet chairs is preparing and cutting the raw materials. As shown in the image, a worker operates a machine that processes metal tubes. These tubes are likely being cut or shaped to form the chair’s frame. Water or moisture on the metal Components. It shows that coolant or lubricating fluids were used during cutting.
-
Prevents overheating: Coolant prevents overheating by dissipating heat from friction during metal cutting.
-
Reduces equipment wear: These fluids reduce wear on the cutting tools. It will help them last longer.
-
Provides a smoother surface: Lubrication provides a smoother surface by reducing imperfections. It prepares the metal for the next production steps.
After cutting, the parts are checked to make sure they meet the right size and quality standards. Once approved, we move on to the next stage of production.
Bending
After cutting, the metal tubes are bent to shape parts of the chair frame. As seen in the image, the worker is operating a bending machine to achieve the required shapes. This step is essential for creating consistent angles and maintaining structural integrity. Bending also allows the components to fit precisely during assembly.
-
Ensures accurate shapes: Properly controlled bending prevents cracks or weaknesses from forming.
-
Prevents material fatigue: Properly controlled bending prevents cracks or weaknesses from forming.
-
Prepares components for assembly:Shaped parts are easier to align. This reduces assembly time and improves stability.
After bending, the components are checked. We will make sure they meet the required specifications. After this, the parts are ready for the next steps, such as drilling or welding.
Drilling and Welding
After bending, the production process moves on to drilling and welding. These steps are essential for assembling the banquet chair components. They ensure both functionality and durability.
Drilling
Drilling makes precise holes in the metal frame for screws, bolts, or other fasteners. As seen in the image, a worker operates a drill press to process square tubes. This step ensures that frame components align perfectly during assembly. Key purposes of drilling include:
-
Alignment for assembly: Holes are accurately positioned to make joining with bolts or screws easier.
-
Material preparation for welding: Drilled holes guide where to weld parts or serve as entry points for fasteners.
Welding
After drilling, the components are connected through welding. Robotic welding machines perform this process, ensuring precision and consistency. MIG and TIG welding provide strong, corrosion-resistant joints for durable and aesthetic furniture.
MIG(Metal Inert Gas) | TIG (Tungsten Inert Gas)
Key Purposes of Welding
-
Structural Integrity: Proper welding makes joints as strong as the base material. It prevents detachment or failure under load. This ensures the chair frame can handle frequent use and pressure. It is especially important in high-traffic environments like banquet halls.
-
Durability: High-quality welds remove weak points. It helps the furniture withstand bending and vibration over time. TIG welding enhances corrosion resistance, especially for stainless steel. Additionally, TIG welding is often used for stainless steel to enhance corrosion resistance.
-
Aesthetic Appeal: Neat, smooth welds reduce the need for extra surface treatment, creating a sleek and polished look. This is especially important for furniture, where both form and function matter.
Important Considerations in Welding
-
Heat Control: Excessive heat can deform metal or weaken the joints. Robotic welding helps maintain consistent heat input. This ensures uniform weld quality across multiple components.
-
Safety Measures: Welding produces hazardous fumes, heat, and light. Proper ventilation, protective equipment, and fire safety protocols are essential. They protect workers from burns, fumes, and flashes.
-
Quality Control: Non-destructive testing (NDT) checks for defects like cracks or porosity. These defects could weaken the stability of the furniture. This ensures that every weld meets the required standards.
After welding, inspections check the alignment and strength of the joints. RON GROUP runs quality checks at every stage to make sure the product meets high standards. This approach ensures smooth coating and assembly, leading to reliable, high-quality furniture.
Deburring
Next is deburring, which removes sharp edges, burrs, and imperfections from metal parts after drilling or welding. In the image, a worker smooths the edges of a chair frame to ensure safety and a high-quality finish. Deburring has two purposes. It prevents injuries during handling and assembly. It also improves appearance by reducing the need for extra touch-ups before painting or coating.
Manual Deburring for Precision
Due to variations in product designs, manual deburring is commonly employed at this stage. Experienced specialists use files, grinding wheels, and polishing machines to smooth out imperfections. This ensures accuracy, even in complex shapes. Careful attention is needed to avoid damaging the components while achieving a smooth finish. The remaining flaws can disrupt the coating process. This makes it difficult to produce furniture that is both high-quality and visually appealing.
Proper deburring ensures smooth coating or assembly, improving the product's appearance and durability.
Degreasing
Degreasing in powder coating removes oils, dirt, and residues to ensure the coating sticks well. Without proper cleaning, contaminants can cause peeling, bubbles, or rough spots. It reduces durability and appearance.
The type of metal determines whether to use alkaline or neutral degreasing agents. Steel parts often collect machine oils during fabrication. So they need intensive cleaning, such as immersion or spray methods, to remove all residues.
The Purpose of Degreasing
-
Improves Adhesion: Degreasing removes oils and dirt to help the coating stick better and prevent peeling or flaking.
-
Prevents Corrosion: It also prevents moisture from getting trapped under the coating, which could cause rust over time.
-
Enhances Finish Quality: A clean surface makes the coating smooth and even, with fewer bubbles or rough spots.
-
Extends Product Lifespan: Good degreasing makes the coating last longer by protecting it from weather and wear.
Steps in the Degreasing Process
-
Pre-cleaning: The metal surface is first wiped or rinsed to remove loose dirt and debris.
-
Application of Cleaning Agents: Alkaline or neutral cleaners are used to remove oils and other contaminants. They are applied through immersion or spray methods on the metal surface.
-
Rinsing: The parts are rinsed well to remove any leftover cleaning agents. This makes sure no residues are left that could affect the coating.
-
Optional Phosphating: In some cases, a phosphating step is added after degreasing. It improves corrosion resistance and enhances adhesion before the powder application.
-
Drying: Finally, the metal parts are dried completely to prepare them for the next steps, such as sandblasting or powder coating.
The images show metal frames grouped and hung on a conveyor for immersion degreasing. The worker makes sure the parts are fully dipped in the cleaning solution to remove oils and residues from manufacturing. This careful pre-treatment gets the parts ready for powder coating, helping the final product to be durable and look perfect.
Powder Coating
In powder coating, banquet chairs and metal furniture go through several layers to ensure they last long, look good, and resist rust. Here is a quick look at the coating layers and what they do:
Primer Layer
The first layer usually involves applying a primer, especially for metals like steel that are prone to corrosion. The primer helps the coating stick to the metal, protects against rust, and prevents peeling or flaking.
Top Coat
After the primer, a top coat is applied to provide color, texture, and additional protection. It can have different finishes, from matte to high gloss, and includes UV protection to keep the product looking good over time. For outdoor or heavy-use furniture, this layer is important to make it durable and resistant to weather and wear.
Optional Clear Coat
Sometimes, a clear coat is added on top for extra protection from scratches, impacts, and chemicals. This coating extends the lifespan of the finish and is often used for heavy-duty furniture or items exposed to harsh environments.
These layers help the furniture last longer and stay looking good, making powder coating a popular finish for metal furniture.
Curing
After the powder is applied, the parts go into a curing oven, where heat hardens the coating. This step is important because it turns the powder into a strong, lasting finish that looks good and protects the surface.
Stages of the Curing Process
-
Heating: Once inside the oven, the temperature gradually rises to around 150°C to 230°C (300°F to 450°F), depending on the type of powder used. The heat is absorbed by the metal substrate, transferring it to the powder coating.
-
Melting and Flowing: As the heat increases, the powder melts and flows into a uniform film, ensuring smooth coverage across the surface of the furniture frame.
-
Chemical Crosslinking: The resin in the powder reacts through a process called crosslinking. It makes the coating stronger. This stage is essential for forming a scratch-resistant and chip-resistant finish.
-
Cooling: After curing, the parts cool down, turning the coating into a hard, durable layer that can handle weather and daily use.
A well-controlled curing process makes the product resistant to scratches, rust, and wear. The oven’s efficiency, along with proper temperature and timing. It prevents problems like undercured coatings that can cause brittle finishes or weak adhesion.
RON GROUP follows precise curing guidelines to give the metal furniture both strength and a good look. This makes sure it is high-quality and lasts a long time.
Conclusion
This article focused on the structural aspects of metal furniture production, particularly the creation of strong frames for banquet chairs. When it comes to adding backrests and seat cushions, the assembly and decoration techniques share similarities with those used in wooden furniture. If you're interested in these steps, keep an eye out for our upcoming blog on "Wooden Furniture production", where we will explore them in detail.
To see the full metal furniture production process in action, check out our video on YouTube: Restaurant furniture customization. We hope you enjoyed this walkthrough and encourage you to explore more of our content!
If you’re curious about our other production processes, take a look at our Factory Showcase. There, you can explore how we manufacture other products and gain a broader view of our company’s capabilities.
The following image shows some of the finished products from our metal furniture line. If you are interested, feel free to explore more on our website: RON GROUP Restaurant Furniture Collection.
Get the week's latest industry information
-
Real-Life Professional Restaurant Case Studies
-
Create a unique restaurant with over 95,700+products
-
Protessional Free 3D Restaurant Design
-
Still Have Questions About Opening a Restaurant?
Discover Our Exclusive Products
Explore our extensive range of restaurant and hotel supplies designed to enhance your operations. Find the perfect solutions to meet your needs.
Browse Our ProductsFREE 3D DESIGN
Boost your restaurant's success with our free 3D design service. Start building the restaurant of your dreams today!
Explore 3D Design Case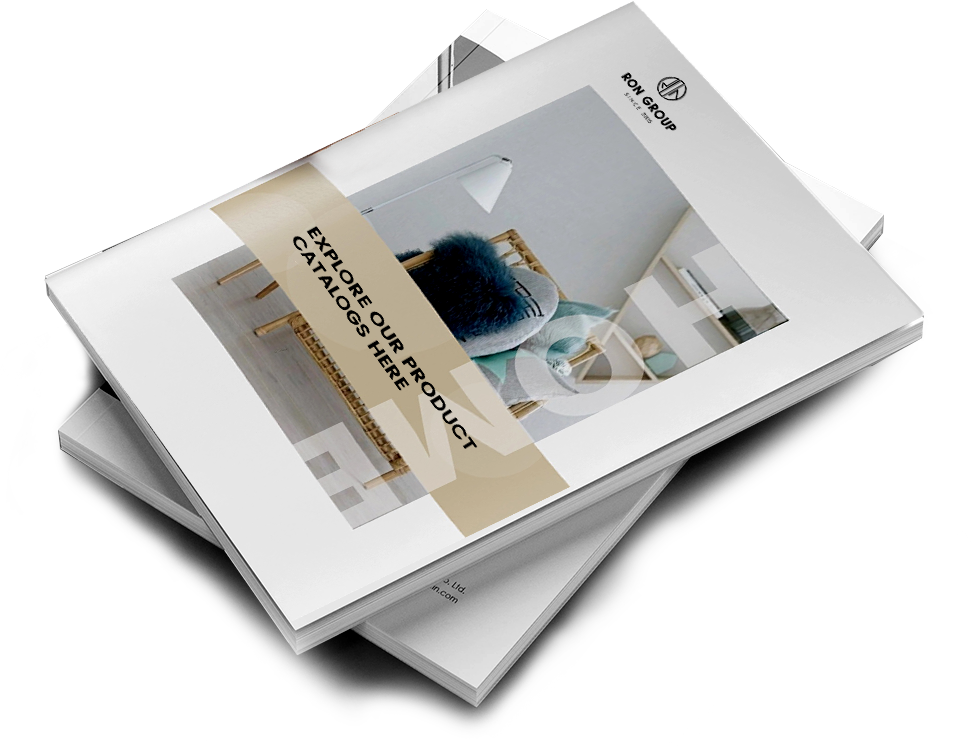
RECOMMENDED CASES
-
Mo’s Seafood and Chowder Finds Unique Brand Identity with Custom Platters from RON GROUP
RON GROUP's custom fish-shaped platter strengthened Mo’s brand and elevated the dining experience
Learn More -
Maison Mai: Your Guide to Opening a Restaurant – From Design to Reality with Premium Furniture
RON GROUP provides Madamemai's Maison Mai with seamless one-stop design and customization solutions
Learn More
RECOMMENDED BLOGS
-
5 Mistakes to Avoid When Buying Restaurant Furniture from China
Don't fall for costly oversights! Learn the 5 mistakes to avoid when buying restaurant furniture from China and ensure a...
Ron2025-01-079 min read -
RON GROUP Launches VR Experience to Explore Our Dynamic Showroom
Discover RON GROUP's VR showroom! Explore dining furniture, tableware, and customized services virtually or visit us in person to...
Sylvia2024-12-163 min read -
Building a Global Network: Ron Group's Restaurant Collaborations
Ron Group expands its global network with partnerships like Doju and Fonda Argentina, offering diverse dining experiences...
Sylvia2024-11-2910 min read
Subscribe to RON GROUP
Stay up-to-date with the latest industry insights and expert advice. Together, we'll create your ideal restaurant.
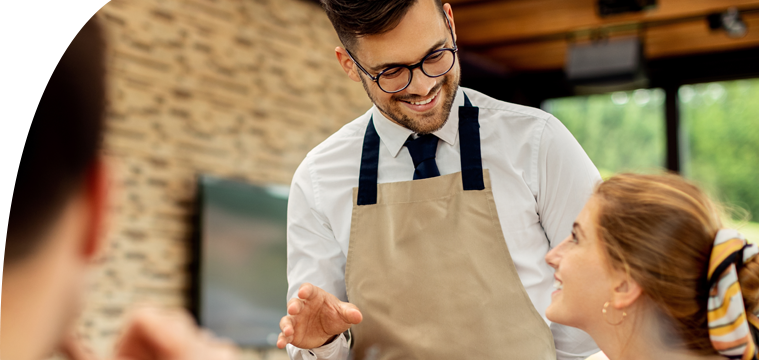