Content
Introduction
Wood furniture has maintained a strong position in the global market. It fits well with a variety of interior styles, making it a popular choice for homes, offices, and commercial spaces. Wood furniture covers a wide range of styles. You can choose from luxurious solid wood or cost-effective engineered pieces to find what suits your needs.
This article provides a step-by-step look at how RON GROUP produces wood furniture. From selecting the raw materials to applying the final touches.
Wood Classification
The classification of wood for furniture making is based on three main factors: shape, type, and size. These categories help manufacturers pick the right wood for their needs. They consider factors like quality, cost, and strength.
1. By Shape
Category | Characteristics | Applications in Furniture Making |
---|---|---|
Logs | Unprocessed wood in its natural form | Used for high-end rustic furniture, such as live-edge tables, carved pieces, and artisanal designs |
Square Timber | Rectangular or square cross-section | Commonly used for furniture frames, including bed frames, table legs, and sofa structures |
Planks/Boards | Wide and thin; typically used as surface material | Ideal for tabletops, cabinet doors, wardrobe panels, and bookshelves |
Wood Rods and Poles | Cylindrical in shape | Used for chair legs, armrests, garment rods, kids’ furniture, and decorative accents |
Wood Chips | Irregular small pieces | Used as filler material or for decorative purposes, such as particleboard cores or composite panels |
Plywood | Made from multiple layers of wood veneer glued together | Great for backs, drawer bottoms, cabinetry, and lightweight furniture parts |
Wood Strips/Batons | Thin and narrow pieces | Used for joints, trim work, and structural reinforcements in furniture |
Bent Wood | Wood steamed or chemically treated to create curved shapes | Perfect for artistic furniture, such as bentwood chairs, rocking chairs, and sculptural designs |
2. By Species
Different wood species influence the look, strength, and cost of furniture.
Hardwoods: Durable woods like oak, walnut, and mahogany, often used for premium furniture.
Softwoods: Pine and cedar are lightweight and affordable but less durable over time.
Engineered Wood: MDF and plywood offer cost-effective options for large-scale production.
3. By Size and Thickness
Thin Boards (e.g., veneers): Ideal for decorative surfaces and finishes.
Thick Panels: Used for structural elements in cabinets and tables.
Dimensional Lumber: Precision-cut wood to minimize waste during manufacturing.
These classifications ensure that manufacturers, like RON GROUP, can select the best type of wood for each product. Controlling size and moisture during processing, such as kiln drying, also prevents warping and cracking in the final product.
Wood Cutting
Cutting is an important step in making wood furniture. It transforms raw wood into parts that fit together perfectly. Depending on the type of project and production volume, RON GROUP uses various tools and machines. This helps improve efficiency, accuracy, and precision.
1. Primary Cutting and Sizing
Sawmilling: Logs are cut into rough planks or panels based on the needed sizes for furniture. This makes the wood easier to work with and helps reduce waste.
Edging and Trimming: After sawing, irregular edges and defects are removed to create cleaner, uniform panels. Trimmers square off the ends of boards, making it easier to align parts in the next stages.
2. Precision Cutting
Manual Cutting: Hand saws and panel saws are used for simple, light, or small jobs. Manual cutting offers flexibility and works well for custom designs. Skilled workers are often required to make detailed adjustments by hand.
CNC Machines: CNC machines handle large volumes, heavy wood pieces, or complex designs. These machines provide consistent accuracy. They can make detailed cuts that are hard to do with manual tools.
Using the right tool for each job makes the manufacturing process more efficient. Manual cutting tools work best for small and flexible tasks. CNC machines are better for heavy workloads and ensuring accuracy for bigger projects.
Drilling
Drilling is important for assembling wooden furniture by making precise holes for joints and fasteners. It ensures stability, alignment, and proper weight distribution across the structure. Depending on the load and design, different drilling techniques and hole types are used.
Types of Drilled Holes
Blind Holes: These do not go all the way through the material. They are ideal for dowel pins, hinges, or hidden connectors, ensuring a clean appearance.
Through Holes: These holes go all the way through the wood and are often used for passing bolts through connected parts.
Countersink Holes: These have a conical opening, allowing screws or bolts to sit flush with the surface. This design improves both aesthetics and functionality.
Drilling Process
Coordinate Setup: Precise alignment is critical to ensure that components fit securely. For example, chair legs need to be perfectly positioned to provide adequate support.
Stabilizing the Workpiece: The wood must be clamped tightly to prevent movement during drilling. This keeps the drilling accurate and prevents damage to the wood.
Joint Type Selection: Choosing the right joint is essential. For furniture that needs to support a lot of weight, like a chair, simple screws (butt joints) aren't strong enough. Stronger connections, such as mortise-and-tenon joints, are required to ensure durability and prevent failure.
The Role of Mortise-and-Tenon Joints
For heavy-duty connections, mortise-and-tenon joints provide superior strength. These joints involve drilling a mortise (slot) into one piece and fitting a tenon (protruding end) from another piece into it. This joint holds the parts tightly together and distributes the weight evenly. It eliminates the need for visible hardware like screws or nails, enhancing both the durability and aesthetic appeal of the furniture.
Sanding
Sanding is an important step in woodworking. It makes surfaces smooth by removing rough spots, imperfections, and old finishes.
Why Sanding Matters
Wood is naturally uneven and may contain surface imperfections. Sanding gets the wood ready for painting, staining, or finishing by smoothing rough spots. It also removes sharp edges, making the furniture safer and look better. For example, rounded corners or smoothed edges prevent potential injuries in everyday use.
Sandpaper Types
Grit Type | Grit Range | Usage |
---|---|---|
Coarse Grit | 40-60 | Used at the start to remove deep scratches, old finishes, or rough surfaces. |
Medium Grit | 80-120 | Smooths out sanding marks and minor imperfections, refining the surface. |
Fine Grit | 150-220+ | Prepares the wood for finishing, leaving a smooth surface ready for paint or stain. |
Choosing the correct grit depends on the roughness of the wood and the desired finish. For example, coarse grit is better for removing old varnish, while finer grits create a polished surface for staining.
The Sanding Process
Inspect and Prepare the Surface: Identify areas that need special attention and secure the wood to prevent movement.
Begin with Coarse Grit: Start with a low grit to remove imperfections, working along the wood grain to avoid scratches.
Progress to Finer Grits: Gradually use finer grits to achieve a smooth, even finish.
Check by Hand: After sanding, run your hand over the surface to feel for any rough patches. Manually sand those areas as needed for a uniform result.
Preliminary Assembly
In the initial stages of furniture assembly, glue and mortise-and-tenon joints play a vital role in securing parts together. These techniques ensure both durability and alignment during the final construction. Here's an overview of how the process typically unfolds.
1. Apply Glue
The inside walls of the mortise (slot) and the tenon (protruding piece) are coated with wood glue to enhance the bond. This glue ensures the parts stay firmly connected and resist future loosening.
2. Insert the Tenon into the Mortise
Carefully fit the tenon into the mortise, ensuring it aligns perfectly. In modern woodworking, glue is used to make joints strong. Some designs, like traditional timber frames, may skip glue to allow the wood to move over time.
3. Secure with Rope or Clamps
Once the parts are joined, ropes or clamps are used to apply even pressure, keeping the components aligned while the glue dries. This technique ensures a tight, stable fit and prevents gaps or misalignment during curing.
4. Check Alignment
For delicate or high-stress areas, it's important to keep the structure square. Ensuring proper alignment during assembly helps maintain strength. If necessary, excess glue is wiped off before it hardens to maintain a clean finish.
This early assembly phase is crucial for stability, especially for furniture under heavy use, such as tables or chairs. Mortise-and-tenon joints are strong and look nice. They spread weight evenly, which makes them better than simple butt joints.
Painting and Finishing
The finishing process is essential to protect furniture from damage and enhance its appearance. Several types of finishes can be applied, each offering unique benefits depending on the desired look and level of durability.
Types of Finishes
Finish Type | Description | Usage |
---|---|---|
Varnish | A clear finish that adds durability and gloss. | Protects against moisture and UV exposure; suitable for both indoor and outdoor furniture. |
Polyurethane | Thicker than varnish, offering more robust protection. | Available in water- and oil-based varieties; ideal for high-traffic surfaces. |
Lacquer | A fast-drying finish with a glossy sheen. | Often sprayed for an even coat; prone to scratches but provides a sleek look. |
Oil Finishes | Tung and linseed oils penetrate wood to enhance the grain. | Creates a smooth, matte finish; requires frequent reapplication to maintain appearance. |
Paint | Provides color and protection in various finishes. | Works well indoors and on exterior pieces with weatherproof coatings. |
Number of Layers
Applying multiple layers of finish ensures durability and a professional look. Here’s a common strategy:
First Layer: Apply a primer or sealer to help the finish adhere properly.
Second Layer: Add the base coat (for paint) or an initial clear coat (for varnish or polyurethane).
Third Layer: Sand lightly between coats to ensure a smooth surface.
Final Layer: Apply the topcoat to seal the finish and provide long-term protection.
The drying and curing times depend on the product used. For example, water-based finishes dry faster, sometimes within two hours, while oil-based finishes may require 24 hours between coats. Following this structured approach helps ensure the furniture remains beautiful and durable for years to come.
Leather Upholstery Installation
Leather upholstery involves several steps to make it both useful and attractive. It usually needs glue, foam padding, fabric or leather, staples, and sewing to create a strong and comfortable finish. Here are the main steps.
Apply Foam and Glue
Start by attaching foam padding to the furniture frame using spray adhesive. The foam provides cushioning and shapes the furniture for added comfort. Batting can also be applied to soften the edges and create a smooth surface before covering it with leather or fabric.
Prepare and Align the Cover
Cut the leather or fabric to fit the piece, ensuring there is enough material to wrap around the frame and foam completely. Pre-sewn panels and piping can enhance the design. Use a sewing machine capable of handling thick leather to sew seams with precision.
Attach with Staples or Tacks
Stretch the material over the frame and secure it using a pneumatic or electric stapler. Start from the center and work outward to avoid wrinkles. Temporary tacks can help ensure proper alignment before final stapling, ensuring a snug and even fit.
Sew and Finish Seams
Use an industrial sewing machine to stitch seams in thicker materials like leather. Machines with high presser feet help manage bulky fabrics. After sewing, trim any excess material for a clean and professional finish.
Check and Adjust
Inspect the piece for any uneven areas or wrinkles. Make final adjustments by stapling loose sections or trimming excess material. Attach a dust cover to the bottom of the furniture to protect the interior components and complete the piece.
Conclusion
Different wood products need specific techniques to make them. Mass production and custom craftsmanship also have different methods. However, the overall process for creating wooden furniture is generally similar to what has been described above. We warmly welcome you to visit and explore these processes in person.
Our primary resources come from videos by RON GROUP, which provide detailed insights into their manufacturing techniques:
If you're looking for furniture suitable for restaurants and hotels, check out these collections from RON GROUP:
Get the week's latest industry information
-
Real-Life Professional Restaurant Case Studies
-
Create a unique restaurant with over 95,700+products
-
Protessional Free 3D Restaurant Design
-
Still Have Questions About Opening a Restaurant?
Discover Our Exclusive Products
Explore our extensive range of restaurant and hotel supplies designed to enhance your operations. Find the perfect solutions to meet your needs.
Browse Our ProductsFREE 3D DESIGN
Boost your restaurant's success with our free 3D design service. Start building the restaurant of your dreams today!
Explore 3D Design Case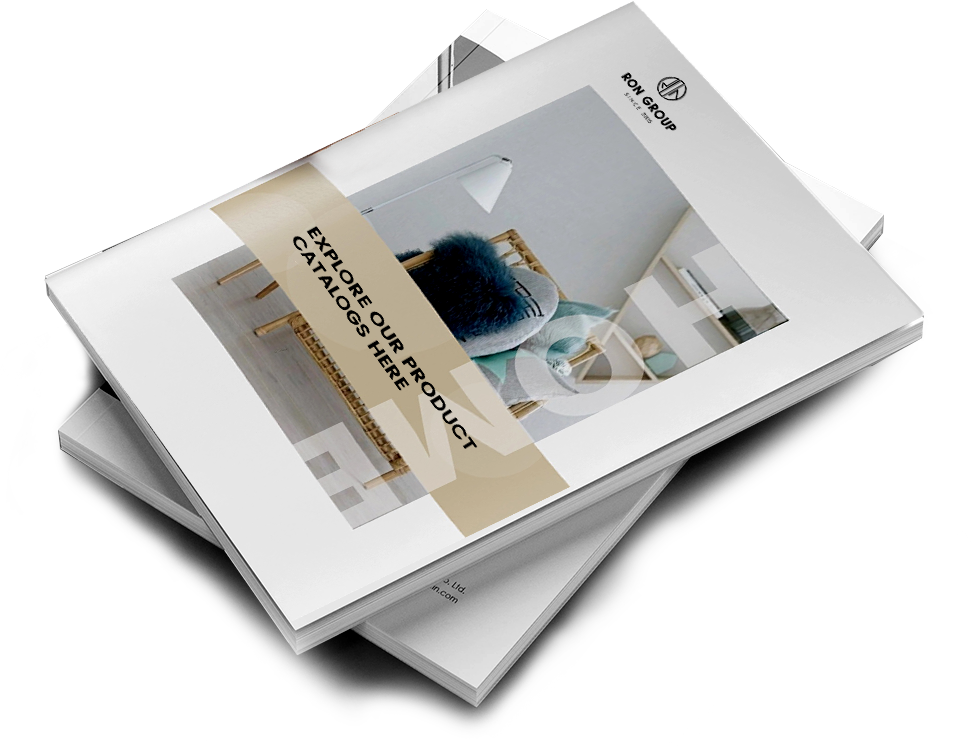
RECOMMENDED CASES
-
Mo’s Seafood and Chowder Finds Unique Brand Identity with Custom Platters from RON GROUP
RON GROUP's custom fish-shaped platter strengthened Mo’s brand and elevated the dining experience
Learn More -
Maison Mai: Your Guide to Opening a Restaurant – From Design to Reality with Premium Furniture
RON GROUP provides Madamemai's Maison Mai with seamless one-stop design and customization solutions
Learn More
RECOMMENDED BLOGS
-
5 Mistakes to Avoid When Buying Restaurant Furniture from China
Don't fall for costly oversights! Learn the 5 mistakes to avoid when buying restaurant furniture from China and ensure a...
Ron2025-01-079 min read -
RON GROUP Launches VR Experience to Explore Our Dynamic Showroom
Discover RON GROUP's VR showroom! Explore dining furniture, tableware, and customized services virtually or visit us in person to...
Sylvia2024-12-163 min read -
Building a Global Network: Ron Group's Restaurant Collaborations
Ron Group expands its global network with partnerships like Doju and Fonda Argentina, offering diverse dining experiences...
Sylvia2024-11-2910 min read
Subscribe to RON GROUP
Stay up-to-date with the latest industry insights and expert advice. Together, we'll create your ideal restaurant.
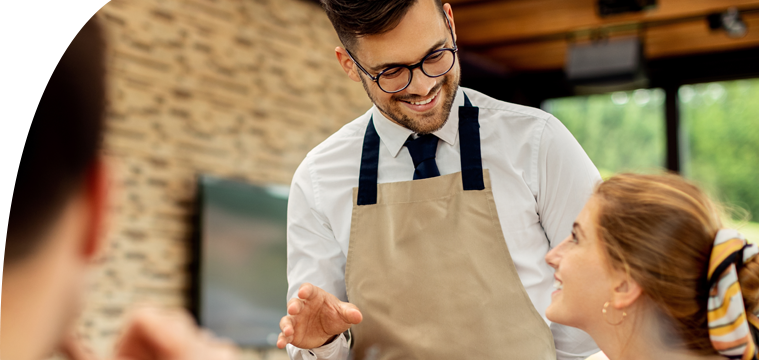